Fully Automatic Filter Press for Dummies
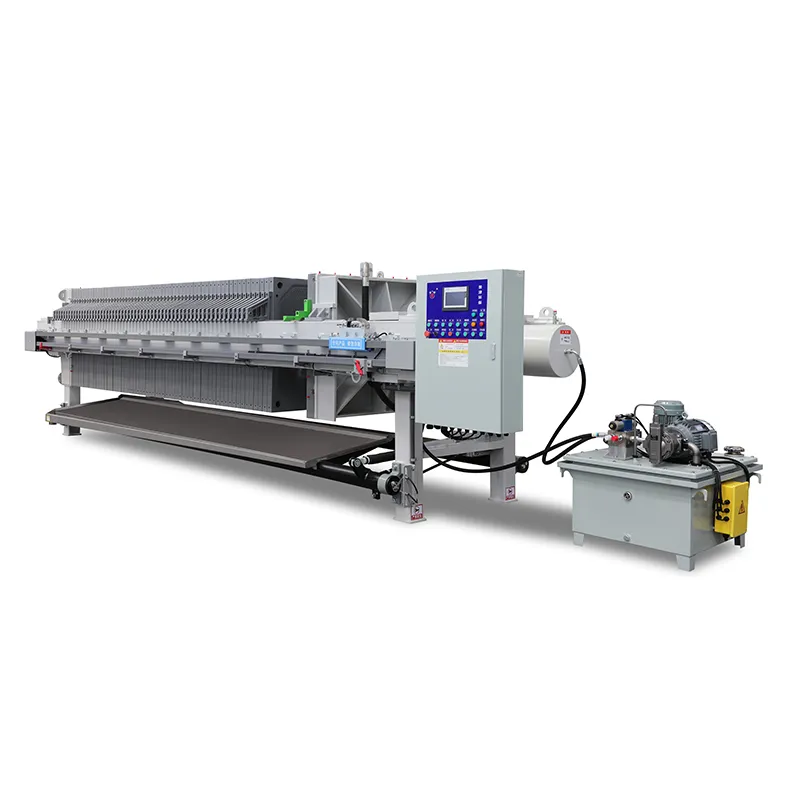
Put into practice a Preventive Servicing Plan: Normal servicing in the hydraulic system, filter plates, along with other components can prevent costly downtime and increase the daily life of the filter press.once the pressing is done, the PLC will control the automatic unloading gadget to get rid of the filter cake around the filter cloth; throughout the full course of action, the PLC will continually keep track of the equipment Procedure status. At the time an irregular scenario is uncovered, for instance overload, quick circuit, etc., the fault alarm and self-protection system might be right away activated to make sure the Risk-free and stable Procedure on the equipment.
Structure of a filter press will depend on a number of factors for example filtration cycle time, cake dryness required, cloth lifetime, regardless of whether handbook or automated plate shifting is ideal, and many other variables.
Micronics models and manufactures industry-leading filter presses in capacities from 2000mm x 2000mm (600 cubic feet) right down to purposeful, lab-scale filter presses such as Micronics MicroPress with one hundred fifty mm filter plates.
Filtration: Once the slurry is inside the filter press, pressure is placed on the system. This pressure is usually produced mechanically or hydraulically. As being the pressure improves, the liquid portion of the slurry is forced to pass through the filtering medium, leaving the sound particles guiding.
Filter presses are used in a wide array of industries due to their flexibility and performance:
Clogging: The filter cloths may become clogged with fine particles, minimizing the performance in the press.
This leads to the solids layer to become denser and forces the filtrate with the filter cloth, in to the channels Within the filter plate, and sooner or later out on the filter Automatic Pressure Filter press.
Since the technologies chief in the area of solid/liquid separation, we and our engineers frequently find to produce new technologies also to place our proven systems to make use of in new parts of application and new markets. In actual fact, we have been in a position to present many new technological innovations lately:
Our equipment, filter presses and candle thickeners are used today in the beet and sugar cane transformation procedures, or in the entire process of refining brown sugar into white sugar.
two.Lessened Downtime: The design allows for swift and straightforward cake discharge, which minimizes downtime in between cycles and will increase Over-all productivity.
The Operating basic principle of filter presses is that slurry is pumped into your machine these types of that solids are dispersed evenly through the fill cycle.
The substitute frequency depends upon the type of slurry and the functioning ailments, but standard inspections may help figure out when replacement is necessary.
We ordered PLC automatic control system from Siemens and Omron. This system adapts system control, reliable and easy, and it is straightforward to work and mend.}